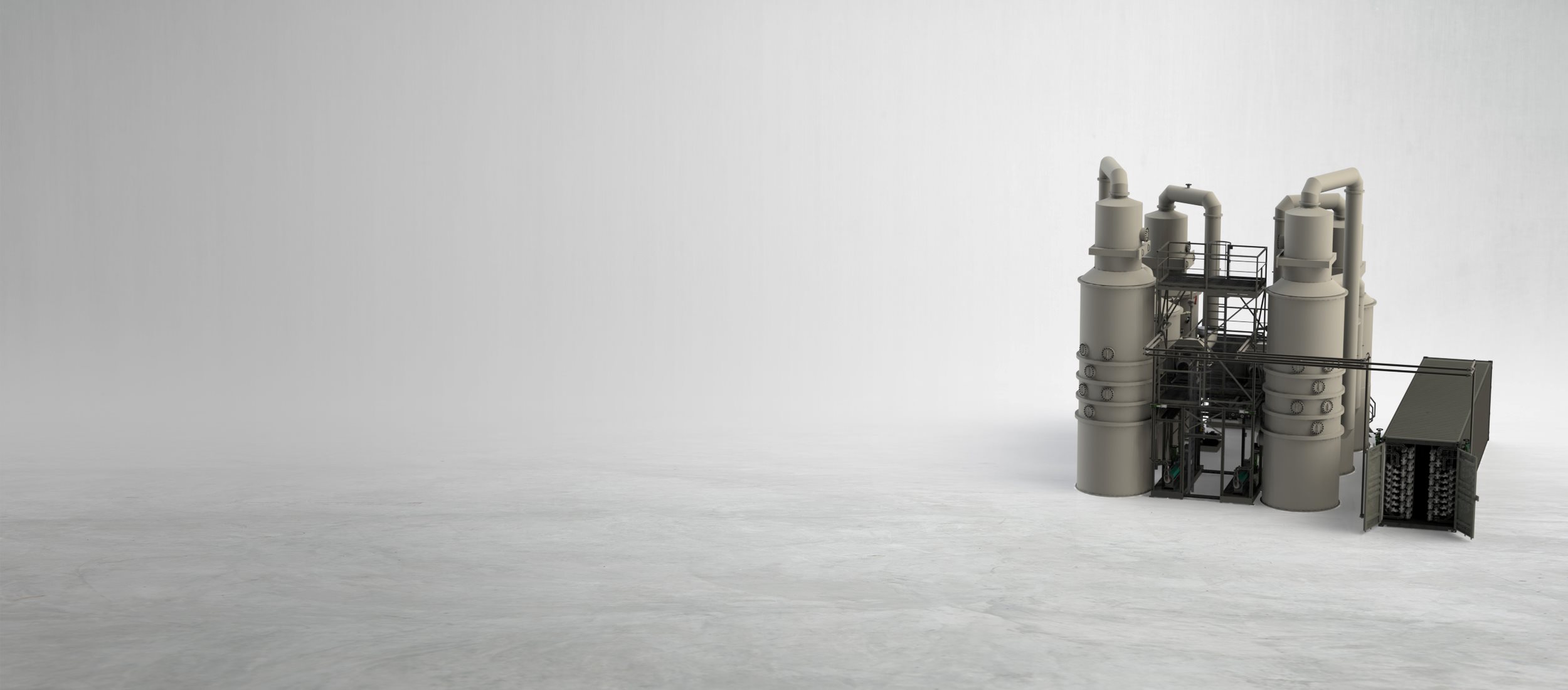
ByoFlex

N-stripping and recovery with ByoFlex®
With the revolutionary ByoFlex® system nitrogen is recovered from highly contaminated substrates. The ByoFlex® system is a one-of-a-kind ammonia stripping unit. Through years of experience, the (ammoniacal) nitrogen stripper has been developed for highly concentrated difficult substrates such as digestate or heavily polluted waste water. Compared to traditional ammonia strippers the system is robust and has a patented, unique design that ensures there hardly is any clogging of the internal parts. Therefore, the stripper can also treat substrates up to 15% dry matter (suspended and dissolved solids) without separation or filtration. Cleaning the ammonia stripper is easy and requires little labour and time.

Process
The substrate is pumped into the top during the ammonia stripping process, where air is blown through the substrate in counterflow mode. Ammonia (NH3) is captured by the air. The air, (partially) saturated with water vapor and ammonia, is blown through a series of 2 ammonia scrubbers. There, the ammonia is removed from the air with sulphuric acid and water to form ammonium sulphate. With the ByoFlex® system a transparent, liquid, pH neutral ammonium sulphate with 8% nitrogen and 40% dry matter is produced. This is a high-quality fertilizer. The clean, yet moist, air is fed back to the stripper. All columns operate at nearly the same temperature.
In a wet environment the gaseous ammonia (NH3) is in equilibrium with ammonium (NH4+). At higher temperatures or higher pH-values the equilibrium shifts to ammonia that can be captured by the air. These 2 parameters are vital for the design of the ammonia stripper.
Prior to entering the ammonia stripper, the substrate is either:
- Heated in a tube-in-tube heat exchanger to elevated temperatures.
- Raised in pH with an alkaline agent (usually not applicable) or after an optional CO2-Stripping
Or a combination of both.
Alternative acids (like ammonium nitrate) can also be used to make other products. Ask us about the possibilities.
The treated substrate leaves the ammonia stripper with low ammonium values, but at almost the same temperature as the incoming fluid. If desired, this heat can be recovered by exchanging incoming and outgoing substrate streams to and from the ammonia stripper. Byosis has developed a special typetube-in-tube heat exchanger, that is 100% modular and demountable, and can be used for heating, heat recovery or cooling.
Ways to use:
Control the ammonium level inside the digester
If the ammonia stripper is installed in a recycle over a digester, it is possible to control the ammonium level in a digester by continuously removing part of the ammonium and using the stripped effluent to dilute the fresh incoming material. This can be done with separated and even non-separated substrate. Using ByoFlex® in this set-up enables you to feed nitrogen-rich materials, such as poultry manure or food waste, without adding water.
This can significantly reduce the cost of the raw material sourcing and/or the disposal costs for your biogas plant, because the volume of effluent to be processed or disposed of is considerably reduced. This improves the revenue model of a biogas plant considerably.
Effluent treatment
The system can also be used as a means of stripping ammonia from wastewater to meet specific nitrogen (ammonia) limits and - in a broader sense - effluent criteria.
As an example, the ByoFlex® system can be used as a pre-treatment system for further processing of the substrates. Especially in combination with biological treatment systems such as a ‘classical’ Nitrification/Denitrification or Membrane Bio Reactor with Reversed Osmosis. Nitrogen elimination is often the limiting factor when dimensioning these techniques and determines the size of the plant, the amount of sludge that is produced and the need for a carbon source for the bacteria. By reducing the ammonium content of the effluent in a ByoFlex® system these systems can be built more compactly, resulting in lower OPEX-costs.
Stripping results
The ammonia stripping efficiency is highly dependent on the temperature of the digestate, the pH level and the electrical energy consumed. In many cases a N-NH4 recovery of 70-75% leads to the an optimum between OPEX- and CAPEX-costs, but higher removal percentages are possible. It may require the use of additional chemicals (usually not applicable), higher temperatures or increased electrical energy consumption. A specific situation determines the optimum design. In most cases, the payback time can be less than 2-3 years!